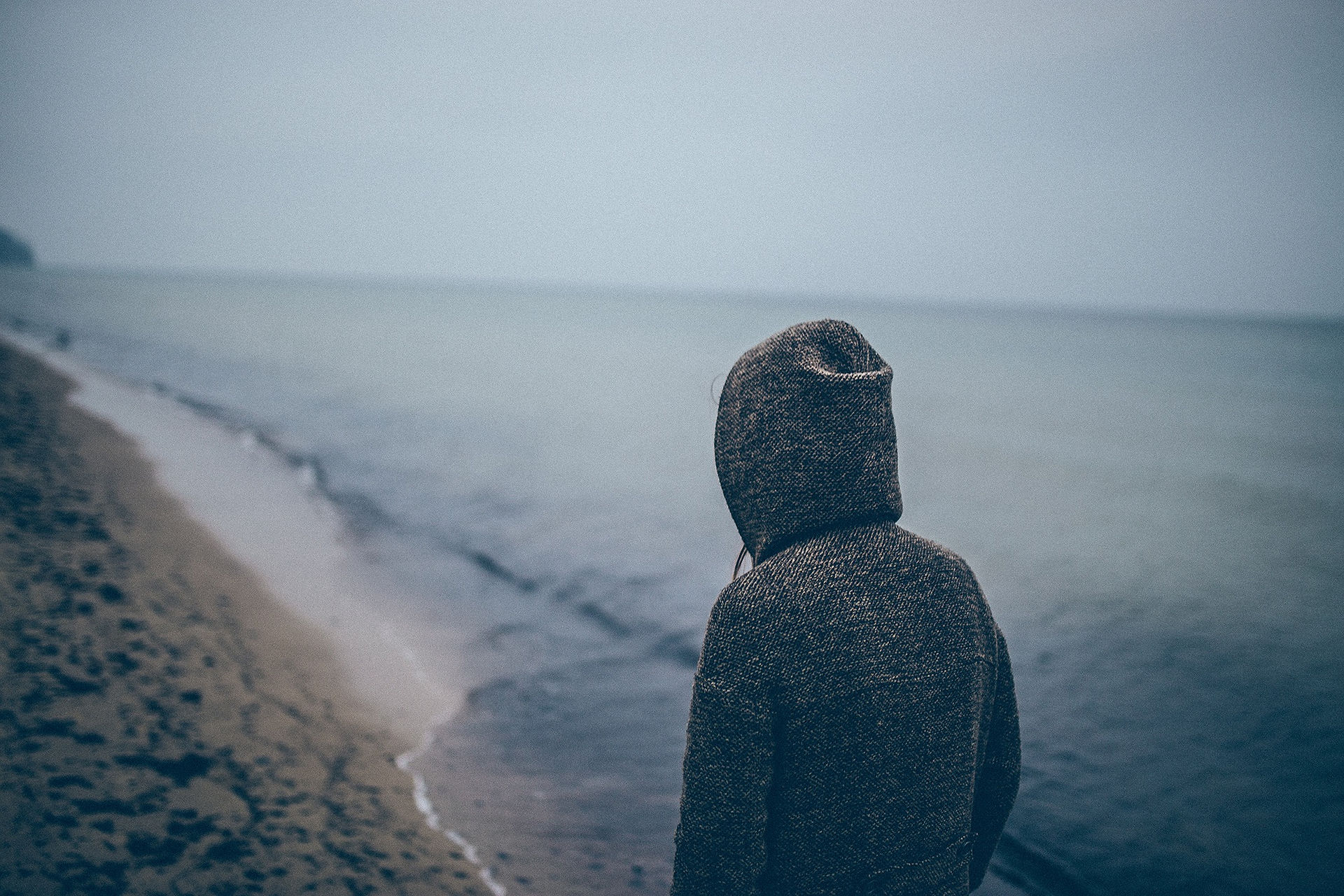

Çelik Çubuk, Boru ve Profil Atölyesi
Mobilya üretiminde akla gelen ilk hammadde ahşaptır.
Ancak günümüzde klasik masif mobilya dışındaki tüm mobilyalarda ahşap malzemenin kullanımı kaybolmaya yakındır.
Mobilya üretimi bugün beyaz eşya ve otomotiv ile aynı yarı mamulleri kullanmaya başlamış neredeyse metal iş kolunda üretim yapar hale gelmiştir.
Çağdaş mobilya parçalarının %90'ı başta çelik, poliüretan, plastik, alüminyum olmak üzere kalıplarla üretilen parçalarıdır.
Ahşap kozmetik bir eleman olarak yüzeyde kaplama olarak kullanılmakta kimi zaman bunun yerini kagıt, film yada boya almaktadır.
Masa tablası veya dolap kapağı gibi ahşabın büyük yüzeylerde kullanıldığı yerlerdeki malzeme ise genellikle ahşap talaşının vinil esaslı tutkallar ile karıstırılması ile elde edilen panellerin kağıt petekler ile beraber kullanılmış halidir.
Modern üretim tesislerinde panel işleme operasyonu tam otomatik makinalarda yapılmaktadır.
Aşağıda metal profil atölyesinde önce kullandığımız hammaddeyi sonra çelik çubuk, boru ve profil atölyesindeki üretim ile ilgili notları ve görselleri bulabilirsiniz.
Aşağıda bulunan Konu Baslıkları
Açık profil çekme(RollForming)
Proje/Teknik Resim/Operasyon Kontrol kartı
1- MALZEME HAMMADDE BILGILERI:
SICAK ÇEKME (Hot Rolling)
Verilen keside göre ısı altında kaba şekillendirilme işlemidir. Sıcak şekillendirme için gerekli özel merdane kalibrasyonları hazırlanır, soğuk şekillendirme öncesi profillerin ana hatlarının oluşturduğu hazırlanma prosesidir.



SOGUK ÇEKME
Sıcak çekilmiş demir kütüklerin tekrardan işleme alınarak çekilme işlemine SOĞUK ÇEKME denir. Soğuk çekme işleminin amacı dayanıklılık, mukavemet, esneklik ve pürüzsüz dış yüzeydir.
SICAK ÇEKİLMİŞ HAMMADDENİN 7 ADIMDA SOĞUK ÇEKİLMİŞ MALZEMEYE DÖNÜŞMESİ:
1. Yüzey temizleme işlemi:
Bu işlem ilk adım olarak sıcak çekilmiş kütüklerin yüzeyindeki istenmeyen kabuk ve çapakları uzaklaştırmak için uygulanır. Yüksek basınçlı demir granülleri yüzeye püskürtülerek yüzey pürüzsüzleştirilir.

2. Çekme işlemi:
Yüzeyi temizlenen kütükleri birinci aşamadan sonra istenen kalibre ölçüsünde çekilmeye hazırlanır. Bunun için malzeme çekim yataklarına yatırılır ve yüzeyleri kayganlaştırıcı maddeyle kaplanır. İstenen ölçü kalıpları yerleştirilir. Kütükler baş kısmından sona doğru çekilerek kalıplardan geçer.
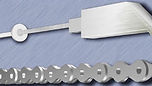
3. Düzleştirme işlemi:
Çekilme işleminden çıkan soğuk çekilmiş malzemenin mukavemeti, rulo ve presler arasından geçirilerek doğrultma işlemiyle sağlanır. Yuvarlak malzemeler buna ek olarak parlatılır.

4. Kesilme işlemi:
Bu aşamada soğuk çekilmiş olan malzeme istenen uzunlukta kesilerek ölçülendirilir.

5. Yuvarlak, altıgen ve kare malzemelerin hazırlanma aşaması:
Bu aşamada milimetrik ölçülerde malzemeye köşeler kazandırılır, aynı zamanda da radius verilebilir. Müşterinin arzusuna göre soğuk çekilmiş malzeme işlenir.

6. Normalize, ısıtma işlemleri:
Soğuk çekilmiş malzemenin özelliklerini arttırmak için uygulanan işlemlerden birisi tekrardan normalize ve malzemenin ısıtılma işlemleridir. Bu işlem esnasında malzemenin dış yüzeyi etkilenmez, aynı pürüzsüzlükte kalır. Sadece malzemenin mukavemeti artar, eğim derecesi yükselir.

7. Kalite kontrol işlemi:
Üretimden çıkan malzeme denetim ve kontrolden geçer. Amaç en yüksek kalitede üretim ve müşteri memnuniyetidir.

Soğuk çekme konusu ile bilginin derlendiği web sayfasına yandaki resim üzerindeki link ile ulaşarak en çok kullanılan ölçüleredeki soguk çekme ürün listelerini görüntülüyebilirsiniz.
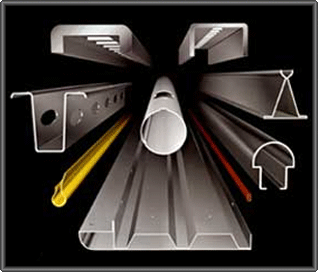


Çelik PROFİL ve BORU NEDİR?
Nasıl Çekilir?
Açık Profil Çekme Hatları
Rollforming Teknolojisi nedir?
Rollforming, genellikle rulo haldeki sacın, rulo açıcıda açılarak, formlandırma kalıbı adı verilen merdaneler ve standlar arasından geçirilerek, istenen kesit ölçülerine ulaşılıncaya kadar, adım adım bükme işlemi olarak adlandırılabilir. Uzun ve çok adetli profil kesitlerinin üretimi için en uygun yöntemdir.

Rollforming’in avantajları nelerdir?
Rollforming, istenen kesitteki profilleri en dar toleranslarda ve sürekli aynı ölçüde üretmeyi sağlar. Hat üzerinde bulunabilecek diğer ilave pres üniteleriyle, delme, şişirme gibi operasyonları da yaparak, üretim zamanında ciddi tasarruf sağlar. Rollform yöntemiyle üretilmişprofiller, diğer yöntemlerle üretilenlere göre daha fazla yapısal dayanıma sahiptir. Diğer yöntemlerle üretilmesi zor olan ince kesitli ve boru formlu profiller üretilebilir.
Rollforming ekonomik bir yöntem midir?
Evet. Rollforming, bir çok firma için hem üretim hızı, hem de genel maliyetler açısından en ekonomik üretim yöntemidir. Özellikle yüksek adetli üretimlerde, sürekli ve yüksek hıza sahip olduğu için Rollforming tercih edilir. Tecrübeli bir Rollforming Hattı üreticisi, profil üzerindeki diğer operasyonları da aynı hat üzerinde çözebileceği için, üretim maliyeti azalır. Kısaca avantajları; daha az aksam , daha az ilave işçilik ve üretim maliyetinde azalma olarak belirtilebilir.

Hangi malzemeler Rollform yapılabilir?
Roll Forming is suitable for almost all metals. Some of the most common are
Rollforming, neredeyse tüm metaller için uygundur. En sık kullanılanlar ise;
1. Galvaniz kaplı sac
2. Paslanmaz Çelik
3. Karbon çelikleri
4. Pirinç
5. Bakır
6. Çinko
7. Titanium – Titanyum olarak söylenebilir.
Diğer yöntemlerden farklı olarak rollforming, boyalı malzemeler için de uygundur.
Her kesit Rollform yapılabilir mi?
Bir çok kesit yapılabilir. Her kesit rollforming için uygun görünmese de, yukarıda gösterilen avantajlarını göz önünde bulundurarak olabilirliğini değerlendirmekte fayda vardır. Bir çok durumda, tecrübeli bir rollform üreticisi, alternatif tasarımlar önerebilir.
Yeni bir parça tasarlamak ve üretmek neye bağlıdır?
Talebe özel rollforming, yaratıcı bir işlemdir. Tecrübeli bir rollform üreticisi, size yol gösterebilir. Maliyetleri azaltmak ve hem üretimi hem de montajı kolaylaştırmak için birçok yeniden tasarım ortaya konabilir.
Rollformla üretilmiş parçalar işçilik ve stok maliyetlerini azaltır mı?
Evet. Rollformla üretilmiş parçalar aynı boyda olacağı için montajda sıkıntı yaratmaz. Bu aynı zamanda üretim alanındaki serbest alanı sağlar ve hurda/fire miktarını azaltır. İlave işlemleri de ortadan kaldırarak işçilikten tasarruf sağlar.
Hangi endüstri alanlarında kullanılır?
Rollformla üretilmiş parçalar her endüstri alanında kullanılabilir. Dar toleranslara ulaşılabildiği için bir çok hassas endüstri rollformu tercih eder.
Borular
Dikişsiz Çelik Çekme Boru
Mobilya üretiminde tercih edilmez. Mobilyada mukavemet ve basınç dayanımı açısından daha düşük dayanımlı dikişli boru kullanılmakla beraber genel bilgi olması amacıyla sanayi boruları hakkında genel bilgiyi bu bölümde bulabilirsiniz.
Mekanik özellikleri sac kıvrılıp kaynak yapılarak üretilmiş dikişli çelik boruya göre haddelenerek ve içi oyularak üretildiği için çok daha yüksek olan, bu nedenle yüksek basınç altında çalışmanın söz konusu olduğu makinelerin yapımında, petrol ve doğal gaz hatlarında, rulman yatakları imalatında, hidrolik sistemlerde ve bunun gibi daha birçok sanayi alanında kullanım alanı bulan bir sanayi borusu çeşididir.
ERDEMİR-ÇELBOR Çelik Çekme Boru Sanayi ve Ticaret A.Ş. Ø26,7 ila 273 mm dış çapları arasında , 2.9 - 40 mm et kalınlıklarında, ASTM A53/A106, DIN 1629/17175, API 5L/5CT/5B Standartlarına uygun Dikişsiz Çelik Çekme Boru üretimi yapan Türkiye'nin ilk firmasıdır. Soğuk Çekme Yöntemi ile (Ø10-114 mm) çapları arasında boru üretimi yapmaktadır.
Bir başka yerli üretici Sardoğan Türkiye Sanayisinin can damarı olan fakat ülkemizde üretilmeyen 60,3 mm ( 2 inch) den 139,7 mm(5 inch) ye kadar mannesman ve soğuk çekme yöntemi ile Dikişsiz Boru üretmektedir.
Ayrıca 16'’ 'e kadar Hidroform üretim metodu ile dirseği kendi imkanlarıyla üretmektedir.
Borçelik BNC Boru adı ile DIN 2448 ölçü standardına uygun olarak, düşük karbon ve alaşımlı çelik malzemeden , 19,0-323,8 mm dış çap ve 2,6 ila 40 mm et kalınlığı arasında üretilen dikişsiz çelik boru üretmektedir.
DIN 2448 ölçü standardına uygun olarak, düşük karbon ve alaşımlı çelik malzemeden ASTM A53, ASTM A106, API 5L, API 5CT, API 5B, DIN 17175, DIN 1629, TSE 381, TSE 301, TSE 346 standartlarına uygun olarak, 19,0-323,8 mm dış çap ve 2,6 ila 40 mm et kalınlığı arasında üretilen dikişsiz çelik borulardır.
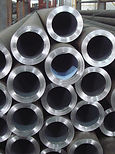
Dikişsiz Çelik Boru Standartları
- API 5L
Bu standarda göre olan borular, genel olarak buhar, su, gaz ve hava hatları için olmak üzere mekanik ve basınç uygulamaları içindir. Bu borular kaynak yapmaya ve kangal yapma, bükme, genişletme vs. gibi şekil vermelere uygundur.
-API 5CT
Casing; petrol ve gaz kuyularına destek için tasarlanmıştır. Borular; petrol ve gaz kaynaklarını çıkartmaktakullanılır. Her bir boru gerilim, yassılaşma ve hidrostatik testlerinden geçirilir. Borular; hidroklorik davranışlar sonucunda kaynakların paslanma başarısızlığını gidermek amacıyla, NACE MR 01-75 dahilinde yüksek dayanıklılıklarda üretilebilir.Borular API monogramıyla desteklenir.
-ASTM A53
Bu standarda göre olan borular, genel olarak buhar, su, gaz ve hava hatları için olmak üzere mekanik ve basınç uygulamaları içindir. Bu borular kaynak yapmaya ve kangal yapma, bükme, genişletme vs. gibi şekil vermelere uygundur.
-ASTM A106
Bu standarda giren borular eğme, ağız genişletme ile benzeri şekil verme işlemlerine ve kaynağa elverişli olmalıdır. Seçilecek kaynak işlemi ile ilgili çelik kalitesine uygun olmalıdır.
-ASTM A179
Bu standart ısı eşanjörleri, kondenserler vb. ısı transfer ünitelerinde kullanılacak minimum et kalınlıklı dikişsiz, soğuk çekme, düşük karbonlu, çelik boruları kapsar. Bu standarda göre olan boruların dış çapları 3,2 mm ile 76,2 mm. (dahil) arasını kapsar.
-ASTM A192
Bu standarda göre olan borular, genelde dış çapı 1/2" ile 7" arasında (12,7 mm. ile 177,8mm.) ve et kalınlıklar 0,085" ile 1,0" arasında (2,2 mm. ile 25,4 mm.) olan dikişsiz çelik çekme boruları kapsar. Borular sıcak çekme veya soğuk çekme olabilir.
-ASTM A333
Bu standart, düşük sıcaklıklarda kullanılmak üzere, nominal dikişsiz ve kaynaklı karbon ve alaşımlı çelik boruları kapsar. Bazı ürün boyutları, yüksek et kalınlığı düşük sıcaklıklarda basınç yönünden olumsuz etkiler yaratabildiğinden, bu standarda dahil değildir.
-ASTM A519
Bu standart, aşağıda çelik kaliteleri verilen, sıcak çekme veya soğuk çekme olarak imal edilmiş, mekanik kullanım amaçlı dikişsiz çelik boruları kapsar. Kullanılacak kaynak tekniği ve şartları seçilen çelik kalitesine uygun olmalıdır.
-DIN 1629
Bu standart, aşağıda belirtilen alaşımsız çeliklerle imal edilmiş dikişsiz çelik çekme boruları kapsar. Bu borular, kimya fabrikalarının konstrüksiyonunda her çeşit proses ve nakil boruları genel mekanik muhendislik amaçları için kullanılır. maksimum kullanma basıncı ve sıcaklığı tabloda gösterilmiştir.
-DIN 2391
Bu standart, tabloda verilen çelik kalitelerini içeren dikişsiz presizyonlu çelik boruların ebadlarını ve teknik teslimat şartlarını kapsar. bu standarda göre olan borular, hassas ebad toleransları ile düzgün yüzey şartları ve çoğunlukla ince cidarlı boru uygulamarı içindir.
-DIN 2448
Bu standart DIN 1629, DIN 17172 ve DIN 17175 standartlarının teslimat teknik şartlarına göre vgerilecek borulara ilişkin ebad ve birim ağırlıklarının tesbitinde kullanılır. Ancak DIN 2391'e göre olan presizyonlu borulara uygulanmaz.
Dikişsiz Boru Kullanım Alanları
1. PANEL ve DAVLUMBAZ BORULARI
Ø 2-4 ¨ dış çapları arasında, muhtelif et kalınlıklarında DIN 17175 standardına uygun St.35.8, St 45.8 ve 15Mo3 kalite çelikler kullanılarak üretilen ısıya dayanıklı borulardır.
2. KAZAN BORULARI
750 °C sıcaklığa kadar çalışabilen kazanlarda süper heater ve eşanjörlerde kullanılan min.1/2 ¨ çapında DIN 17175 standardına uygun St 35.8, St 45.8, 15Mo3, 13CrMo44 ve 10CrM910 kalite çelikler kullanılarak üretilen borulardır.
3. PETROL VE SONDAJ BORULARI (OCTG- Oil Country Tubular Goods)
Sondaj kuyularında muhafaza (kolon-casing) ve üretim (tubing) ve manşon (coupling) olarak API 5CT standardına uygun H40, J55, K55 ve N80 kalite çelikler kullanılarak, API 5B standardına uygun dişli-manşonlu olarak üretilen borulardır.
4. HAT BORULARI (OCTG)
API 5L standardına uygun olarak, kaynak ağızlı veya API 5B standardına uygun olarak dişli-manşonlu olarak Grade A ve Grade B kalite çelikler kullanılarak üretilen borulardır.
5. MEKANİK AMAÇLAR İÇİN KULLANILAN BORULAR
Otomotiv sanayinde, hidrolik sistemlerde, vagon imalat sanayinde ve zirai aletler sanayinde kullanılan, DIN 1629 standardına uygun St 52 ve özel amaçlar için geliştirilmiş 24Mn4 kalite çeliklerden üretilen borulardır.
6. BASINÇLI KAP ( TÜP ) İMALATINDA KULLANILAN BORULAR
İçinde basınçlı gazlar (Co2,O2,N,vb) ve yangın söndürme kimyasalları depolanan yüksek basınca dayanıklı tüp imalatında gövde olarak kullanılan, 32CrM04, DIN 1629 standardına uygun St 52 ve API 5CT standardına uygun J55 kalite çelikler ile üretilen borulardır.
7. SIVI,GAZ ve TANE İLETİM AMACI İLE KULLANILAN BORULAR
Genel amaçlı olarak sıvı, gaz ve tane iletimi amacıyla TS 301, TS 346, TS 381, ASTM A53, ASTM 106, API 5L, API 5CT, DIN 1629 ve DIN 17175 standartlarına uygun olarak üretilen borular.
8. PROFİL BORULAR
Genel amaçlar ve makine parçaları için muhtelif kalite çelikler kullanılarak üretilen kare, dikdörtgen ve özel kesitli profillerdir.
9. ASKERİ AMAÇLAR İÇİN KULLANILAN BORULAR
Özel standartlara uygun çelikler ile üretilen bomba gövdesi, roket gövdesi, mermi kovanı, palet ve gömlek olarak kullanılan askeri amaçlı borulardır.
SICAK ÇEKME DİKİŞSİZ BORULARIN VE PROFİLLERİN KULLANIM AVANTAJLARI
Dikişli borularla elde edilemeyen yüksek mukavemet ve yüksek sıcaklık ve yüksek basıncın elzem olduğu alanlarda Makine parçası olarak dolu kütükten işlemek yerine daha az işçilik ve maliyetlerle üretim yapılması Kalın etli çelik çekme borulardan sağlam Konstrüksiyon imalatında düşük maliyet
Dikişli Çelik Borular

Dikişli borular genel olarak :
-
ERW Su Boruları
-
SRM Borular
-
ERW Doğalgaz Boruları
-
Polietilen Kaplı Borular
-
Kazan Boruları
-
Sanayi Boruları
-
Özel Şekilli Profiller
-
Çekme Borular
-
Yangın-Yivli Borular
-
Sera Boruları
-
Beton Borusu
-
Gemi Borusu
olarak sınıflandırılır.Bizim ilgi alanımız bu grup içerisinden sanayi borularıdır.

Sanayi Boruları
Üretim Aralığı
-
Dış Çap: 5 mm-83 mm
-
Et Kalınlığı: 0.70 mm- 3.50 mm
-
Boy: Boru boyu standart 6 m'dir. Özel siparişlerde istenen boyda teslim edilebilir.
-
İç Çapak Alma: 22 mm ve üstü iç çaptan, iç çapak alınabilmektedir.
Üretim Standartları
DIN 2394, BS 6323 PART 5, EN 10305-3
*Sanayi boruları; istek üzerine değişik kalitede, sıcak haddelenmiş, dekape edilmiş ya da soğuk haddelenmiş bantlardan yüzeyleri, kromaj ve benzeri uygulamalara uygun şekilde üretilmektedir.
Aşagıdaki linklerde borusana ait standart üretim tabloları mevcuttur.
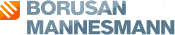
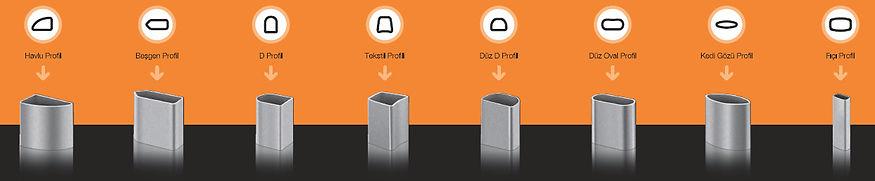

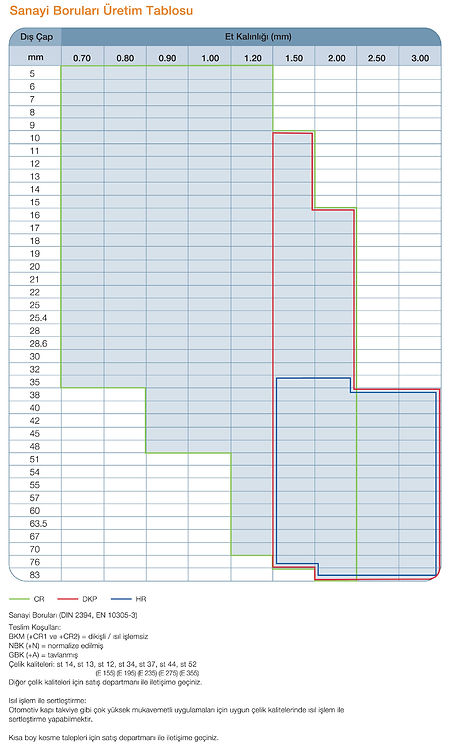
Boru ve Profil İmalat Hatları
Kısaca rollforming hattının finişinde alın kaynak yaparak profilin borunun kapatılması olarak tariflenebileceği gibi teşkilatı tam bir üretim hattı Rulodan sacı dilme dogrultma, formlama ve kalibre vs. operasyonlarını içeren
Aşagıdaki Ünitelerden oluşur.
- Döner Bant Boşaltma Üniteleri
- Bant Doğrultma Makinaları
- Bant Uç Kesme ve Kaynak Masası
- Yatay ve Düşey Akümülasyon Üniteleri
- Boru Makinası Form ve Kalibre Pasajları
- Kaynak Sonrası Dış Çapak Alma Tertibatları
- Boru Soğutma Ünitesi
- Boru Doğrultma Pasajları
- Profil Pasajları
- Uçan Testereler
- Boru Makinası Çıkış Konveyörleri
- Kayışlı Motorize Boru Biriktirme Hendekleri
- Spiral Boru Sanayi Münferit Ekipmanları
Boru Finişing Hatları
- Havşa Üniteleri
- Diş Açma Üniteleri
- Boru Ve Profil Doğrultma Makinaları
- Boru Hidrostatik Test Makinaları
- Boru Galvaniz Tesisleri
- Boru Paketleme Üniteleri
- Boru Transfer Konveyörleri
- Boru Tav Fırını
- Çelik Konstrüksiyonu Isıtıcılı Boru Fosfatlama ve Reaktif Yağlama Tankları
2- METOD / İŞLETME BILGILERI:
Üretimde Kalite ve Verimlilik
Süreklik ve sistematik kurgusu ;
Üretim yapılması için şart işin üretim öncesinde tanımlı olmasıdır.
Tanımlayamadığınız bir işi gerçekleştirmek tesadüflere bağlıdır. Tanımlama ölçülebilir ve nesnel şartlara bağlı olmak zorundadır.
Verimliliğin sağlanması için tanımlı iş, tanımlı sürede, tanımlı istasyonda yapılmalıdır.Ancak bu tanımlamaların doğruluğunu sağlayabilirsek işi yapan personelin verimliliğinin ölçümü yapılabilir.
Üretimde bu tanımlamada kullanılan araç TEKNİK RESİM ve baglı bulundugu sistem dahilinde malzeme ile beraber dolaşan OPERASYON KONTROL/ONAY KARTLARIdır.
Tanımlı işi tanımlı istasyonlarda yaparken izlenen rota (operasyonlar) SÜREÇ ŞEMALARI yardımı ile masa üzerine yatırılır ve eş zaman optimizasyonu yapılarak personel sayısı ve istasyona göre zaman dengeleme çalışması yapılır.
Akışı engelleyen unsurlar tesbit edilir, kalite ve verim için işin tamamı göz önüne alınarak şartlar düzenlenir. Sonraki çalışmalar ile bu düzen sürekli geliştirilir, hedef en az aksiyon ile en yüksek verime ulaşmaktır.
Görev ve sorumlulukları verilen personelin istasyonlara göre dağılımının ve kapasitelerinin bilinmesi şarttır. Bu takip PERSONEL ŞEMASI üzerinde sürekli güncellenerek değişen şartlara göre minimum personel sayısı hedefi takip edilir.
Aşağıda bu iki şemanın örneklerini görebilirsiniz.



Üretim tesislerinin yerleşimi ve malzeme elleçleme sistemleri bir şirketin üretkenliği ve karlılığını etkileyen en önemli kararlardandır.
Yerleşim (layout) derken üretim makine ve donanımları, iş istasyonları, insanlar, her türden ve safhadan malzemelerin bekleme alanları ve malzeme elleçleme sistemlerinin fiziksel düzenlenmesinden bahsetmekteyiz. Her yeni tesis mutlaka bir ELLEÇLEME YERLEŞİM ÇALIŞMASIna ihtiyaç duyacaktır.
Aşagıda örnek bir çalışma görselleri ve sonuçları mevcuttur.
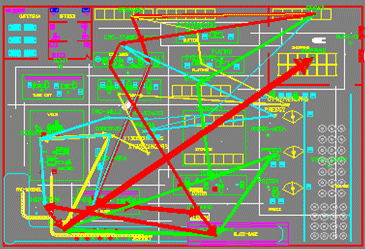
Yukarıdaki resimde kötü bir yerleşim ve kötü bir iş akışı bulunmaktadır. Sadece mazleme depolarının doğru yerleştirilmemesi bile bu tarz bir sonucu yaşamak zorunda bırakabilir.
Ayrıca mevcut tesislerde ürün, malzeme veya süreçlerdeki değişimlerden ötürü ortalama her 18 ayda bir kapsamlı bir yeniden yerleşim planlaması güncellenmelidir.
Malzeme elleçleme, malzemenin bir yerden diğer bir yere taşınması anlamına gelir ki günümüzde tesislerde yoğun bir işgücünün yorucu taşıma görevlerinde kullanılma ihtiyacı modern malzeme elleçleme donanımları sayesinde ortadan kalkmıştır. Genel kural olarak malzeme elleçleme sistemlerine yapılacak yatırımın en fazla 2 yıl içerisinde (başka bir deyişle %50 ROI’ye sahip olmalı) işgücü, malzeme ve yönetim giderlerinden yapılacak tasarrufla kendi maliyetini karşılaması gerekmekte.
Bu noktada gereken üretilecek ürünün süreç haritasına göre en az yer değiştirmeyi karşılayan (minimum elleçleme) makina/istasyon yerleşim planıdır.
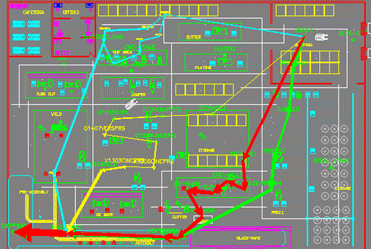
3- OPERASYON BILGILERI:
Ürünü elde etmek için kullanılacak hammadde, makine ve ekipman, personel, üretim metodu işletme içerisinde mevcut olduğunda satın alınarak maliyet haline getirilen tüm bu unsurların hızla ürün haline getirilip maddi karşılığının kazanılması olmalıdır.
Bu kazanımın sağlanması sürecinde;
1.Tanımlanan ürünü elde etmek esastır. Üretimi gerçekleştirmemek dışındaki hiç bir mazeret kalitesiz üretime gerekçe olamaz.
2.Bu üretim süreci içinde hurda oranı minimize edilmeli. Personelin eğitimi neticesinde hurda fire oranları sürekli iyileştirilmelidir.
2.Sonucu fayda yaratmayan boş üretim zamanları minimize edilmelidir.
3.Üretim süreleri ve üretim kabiliyetleri tecrübe edildikçe geliştirilerek en az personel ile en yüksek sayıdaki üretimi gerçekleştirme hedefinde olmalıdır.
Yukarıdaki tüm bu kurgu ile oluşturulan bir atölyede operasyonlar aşagıdaki gibidir.
Yani Biz Çelik Profil Atölyesinde Ne Yapıyoruz....
İşletme maliyetlerini düşürmek isteyen fabrika tasarruf için malzeme elleçleme alanında ne kadar potansiyel olduğu çıkarılmalıdır.
Yukarıdaki örnekte kurulan bilgisayar modelinde yapılan analizler neticesinde malzeme elleçleme maliyetlerinin kabaca hesaplanan değerden aslında %70 daha fazla olduğu ortaya çıktı. Tek başına bu sonuç bile bilgisayar destekli analizlerin önemini ortaya koymakta.
Ardından maliyetleri düşürmek üzere yapılan çalışmalar neticesinde aşağıdaki önlemlerin başarılı şekilde alınabileceği belirlendi;
-
Aşırı yoğunluğa sahip malzeme taşıma yollarının kısaltılması için makinelerin arasında kısa yol oluşturacak yeni koridorlar açılması,
-
Dışarıdan alınan kimi parçaların tedarikçileri tarafından farklı kasa tipi ve kasa içi adetleriyle gönderilmesi sağlanması,
-
Merkezi depo tesis içi küçük depolar şeklinde dağıtılması, Her ne kadar yeni mal kabul kapıları, personeli ve artan IT altyapı gereksinimi gibi yeni maliyetlere rağmen toplamda ulaşılan tasarruf daha büyük oldu.
-
Daha az sayıda forklift ve transpalet kullanmak mümkün oldu. Taşımaya bağlı ürün hasarları ve iş kazaları azaltıldı.
Not:Çizgilerin kalınlığı, o rotadaki malzeme trafiğinin yoğunluğu ile doğru orantılıdır.
Mobilya üretiminde kullanılan çelik çubuk, boru ve profillerin metal atolyelerinde gördükleri işlemler sırası ile
-
Ebatlama,
-
Yüzey polisaj,
-
Form verme,
-
Delme,
-
Kaynak (TIG/MIG/MAG/Punta)
-
Taşlama temizlik polisaj.
1-Ebatlama:



Tanımlı lama, çubuk, profil veya boru açınım ölçüsü fire dahil edilerek ebatlanır.
Bunun için klasik doğrama metodları daire veya şerit testere ile yapılabildiği gibi CNC Makinalar ile boy optimizasyonuda yapılarak firesiz ebatlama yapılmaya çalışılır.
Ebatlama maksadıyla eksantrik preslerde uygun kalıplar yapılarak kullanılabilir bu ebatlama daha çok boru dışındaki geometrilerde kullanılır.Daha seridir.



1ı-Yüzey polisaj:
Ebatlanmış malzeme yüzey ve kaynak dikişinin nefasetine, temizliği göz önüne alınarak yüzey polisaj işlemine sokulur. Genellikle krom kaplama yapılacak borular bu işleme girer.
Otomatik dilme hattına entegre edilen ardışık zımparalardan oluşan işlem otomatik hat ile yapılabileceği gibi manuelde yapılmaktadır.
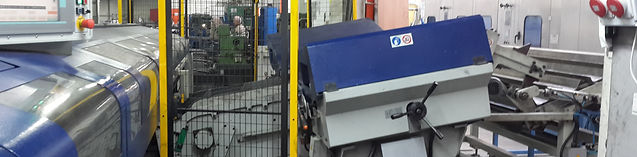

ııı-Plastik şekil verme (Bükme Form):
Boru, profil, ve lama ve çubuk üzerinde yapılan bükme işlemleri büküm şekline göre pres kalıpları ile,makaralı hidrolik bukum makinaları veya Çok kafalı CNC büküm üniteleri ile yapılır.
Benzer şekilde etriye büküm makinası, 3 top profil bukum makinası ve özel amaçlı hidrolik büküm üniteleri kullanılabilir.
Boru bükümünde kritik nokta bükümü malzemeyi kırıştırmadan, zayıflatıp inceltmeden, sıvamadan yapmaktır. Bu maksatla bükülen parca içinden ve dışından desteklenerek bükülür.


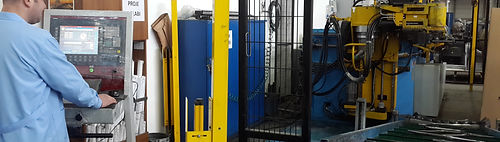

ıv-Profil Delik Operasyonları:
Profiller üzerindeki delikler pres ve kalıp ile kesme yaparak ,matkap veya CNC makinalarda talaşlı imalat ile boşaltılır.
Seri üretim şartlarına en uygun tercih pres operasyonları olmakla beraber kalıp gerekliliği ve düşük miktarlara üretime verimli çözüm olmaması sebebiyle matkap veya freze ile talaşlı üretim tercih edilebilmektedir.
Talaşlı imalat teknik zorunluluklar gereği de tercih edilebilir. Bu durumda işi hızlandırmak için PLC kontrollü sürücüler ve çoklu delme kafalarından destek alınarak aparatlar tasarlanmaktadır.


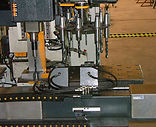
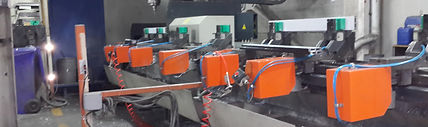
v-Kaynak Operasyonları:
Aşağıda kısa tanımları verilen kaynak türleri ile ilgili dokumanlar pdf olarak üzerine geldiğiniz metine link verilerek bağlanmıştır.
Metal Inert Gaz (MIG):
Argon veya helyum ağırlıklı asal gaz kullanılarak yapılan gaz altı kaynaktır.
Gazaltı ark kaynağında akım ileten teller veya çubuk elektrodlar kullanılır.
Paslanmaz, Aluminyum, Bakır ve tüm metal alaşımlarında kullanılır.
Metal Aktif Gaz (MAG)
CO2 kullanılarak yapılan gaz altı kaynaktır.
Gazaltı ark kaynağında akım ileten teller veya çubuk elektrodlar kullanılır.
Çeliklerin kaynatılmasında kullanılır.
Derin nüfuziyette, hızlı erime ile aralıksız yapılması avantajıdır. Kaynak torcunun yakın olması temiz kaynak yapılmasını kısmen engellediğinden dezavantajıdır.
Tungsten Inert Gaz (TIG/WIG)
Tungsten Inert Gaz yönteminde sürekli elektrod olarak da adlandırılan, erimeyen ve sadece ark taşıyıcı olarak görev yapan elektrodlar kullanılır.
Kaynak ilave malzemesi elektrod değildir.Ya kaynatılacak 2 ayrı parça birbiri üzerine eritilir yada ilave tel besleme yapılarak malzeme kalınlıgı arttırılabilir.
Sert lehim nedir?
Sert lehim ergime derecesi 4500 C ‘ın üzerinde ve ana metallerin ergime derecesinin altında olan ilave metalleri kullanarak ısı yardımıyla birleştirilmeleridir.
Sert lehim Kaynağı Nedir? ve Argon altında TIG yöntemiyle sertlehim kaynağı hakkında döküman.
Aluminyum ve alasimlarinin sert lehimlenmesi
Paslanmaz Çeliklerin Sert Lehimlenmesi
Gerçekten 'paslanmaz çelikler" terimi çok genis çesitlilik arz eden krom içerikli demir esaslı alasımları tanımlamakta kullanılıp bunlar ısı ve korozyona mukavemet aranan uygulamalarda kullanılır. Bugün için bunların sertlehimlenmesi artık bir sıradan is haline gelmistir. İlgili teknik döküman başlığa bağlanmış linktedir.
Paslanmaz Çeliklerin kaynagı hakkında aşagıdaki dökümanlar yardımcı olacaktır.
1-Euro Inox tarafından hazırlanan paslanmaz çeliklerin kaynağı hakkında Hazırlayan :Pierre-Jean CUNAT
2-Askaynak için Can ODABAS tarafından hazırlanan pdf
3-Sarıtaş'ın kısa paslanmaz dokumanı
4-ITU de hazırlanmış Paslmaz kaynak kab ve Schaffler konulu sunum

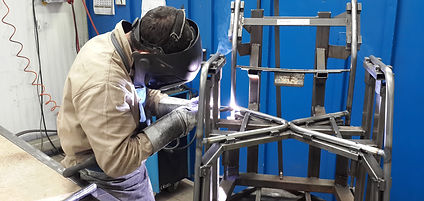
vı-Taşlama Temizlik Polisaj Operasyonları:
MAG Kaynak sonrası parçanın kaynatılan bölgesi el aparatları yardımı ile taşlama, zımpara ve gerekiyorsa moplanarak bütünlüğündeki estetik sağlanır. Taşlama kaynak yapılan bölgedeki tufalıda kaldıracagı için boya veya kaplama hatalarının önüne gecilmesine fayda verir.


Profil atölyesinde üretilen mobilyalara Sandalye, Koltuk iskeletleri, Masa çerçeve ve ayakları seri üretim örnekleridir.

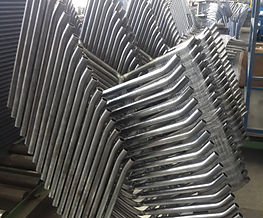
